針對軸承生產企業(yè)套圈生產過程中普遍存在端面缺陷的問題與人工目檢的現(xiàn)狀,下面分享一例基于機器視覺的軸承套圈端面缺陷在線檢測方法。
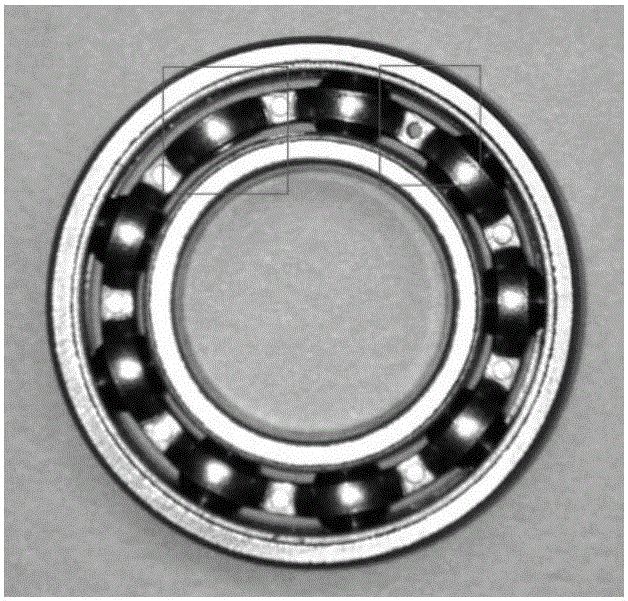
軸承是保證機械裝備回轉精度不可或缺的基礎部件,軸承套圈在經(jīng)過平面磨削加工后,其端面可能依然存在鍛廢、大小邊、磕碰傷、車廢、磨傷、黑皮等外觀缺陷。如果套圈端面存在缺陷,其作為外圓無心磨等后序工位的定位面,勢必影響加工精度和軸承的回轉精度,可能導致軸承使用過程中產生噪聲和振動,從而加速磨損,甚至引發(fā)機器故障。其次,端面缺陷套圈進入后續(xù)工序加工后剔除或成品進入市場后召回,都會給企業(yè)帶來物資與人力成本的極大浪費。因此,必須在平面磨削加工后將缺陷品剔除,避免流入后續(xù)工序。
目前,大多企業(yè)仍憑借質檢員肉眼與主觀經(jīng)驗對套圈進行鑒定與判斷,質檢結果易受人為因素影響,檢驗標準難以保持一致,穩(wěn)定性差且易漏檢。機器視覺具有精度高、效率高、實時性好等優(yōu)點,是替代人工檢測的有效方法。
一:光源選擇與檢測區(qū)域定位
1.1 光源選擇光源是視覺檢測系統(tǒng)不可或缺的組成部分,直接關系到成像質量。良好的照明方式可以凸顯目標區(qū)域的特征,減輕圖像處理工作量。端面缺陷檢測成像面為圓環(huán)形金屬端面,具有一定的鏡面發(fā)射效應,且被測套圈尺寸跨度大,故采用球積分漫反射無影照明方式,照射面積大,光線集中且照射均勻,不會形成鏡面反射,如圖1所示。
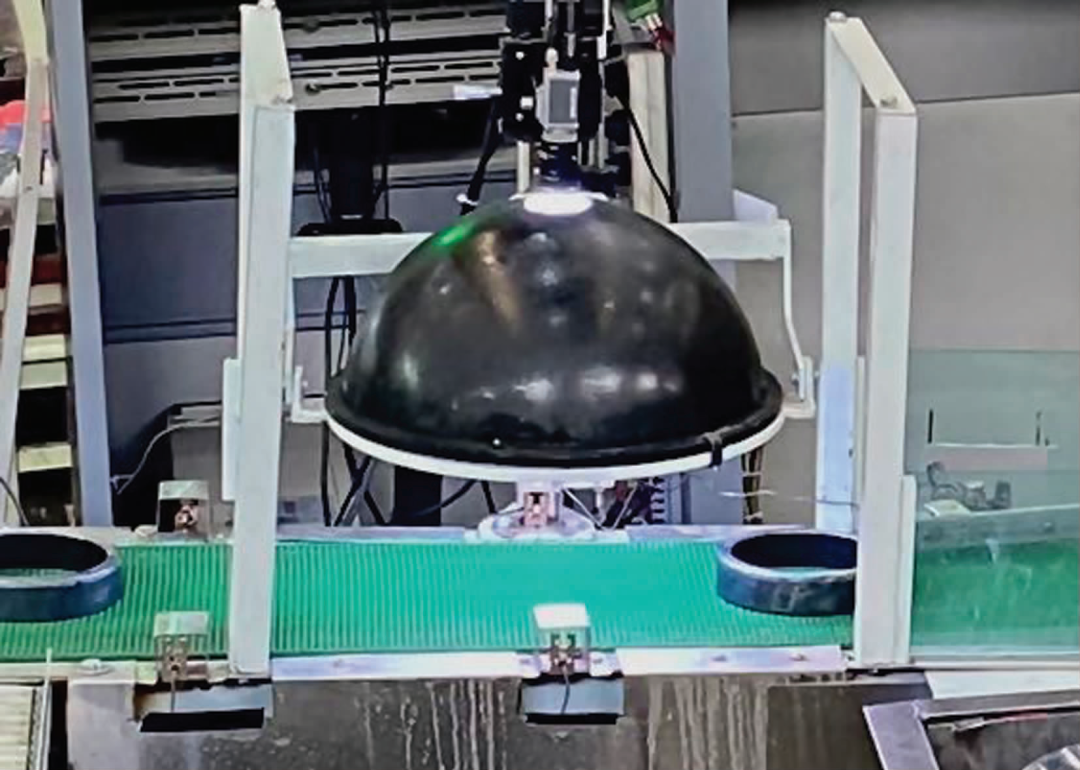
圖1 球積分漫反射無影照明
1.2 圖像預處理圖像捕獲過程中存在的噪聲與干擾會降低圖像質量,增加后續(xù)邊緣檢測與圖像分割的難度因此,需要對原始圖像進行一定的預處理,消除圖像中的噪聲與干擾,均值濾波、高斯濾波、中值濾波的對比效果如圖2所示。由于端面環(huán)形區(qū)域外為背景區(qū)域,灰度值較低,均值濾波處理后的環(huán)形區(qū)域明暗對比變弱,圖像也變得模糊;中值濾波處理后的端面邊緣部分被黑色區(qū)域影響,邊緣細節(jié)丟失;而高斯濾波由于加權平均的特點,在去除噪聲的同時可以很好地保留圓環(huán)及其邊緣的細節(jié)。針對套圈端面區(qū)域與背景區(qū)域對比較大,并且需要檢測出細小缺陷的特點,選取大小為3×3,標準差為1的濾波窗口進行高斯濾波。
1.3 邊緣檢測邊緣檢測是通過識別圖像中亮度發(fā)生明顯變化的部分確定需要識別圖像邊緣的位置。區(qū)域內灰度突變反映了圖像的重要變化,是價值極高的圖像特征。針對本研究,邊緣檢測可以很好地完成套圈端面區(qū)域與背景區(qū)域的劃分,更容易實現(xiàn)檢測區(qū)域的定位,為下一步處理做好準備工作。
1.4 端面定位檢測區(qū)域定位有2種方法:1)對邊緣輪廓進行最小二乘法擬合得到大小圓圓心與半徑,根據(jù)像素點是否在小圓外、大圓內進行端面定位;2)利用四連通域法進行端面區(qū)域定位。大量試驗表明,由于鏡頭畸變和套圈端面倒角的影響,第1種方法偶爾會出現(xiàn)實際端面點沒有包含在擬合端面內的情況,造成誤檢或漏檢,因此本文利用四連通域法進行端面區(qū)域定位。坐標(x,y)處的像素點Р有上下左右4個相鄰像素,坐標分別為(x,y-1),(x,y+1) ,(x–1,y) ,(?x?+1,y),這4個像素點表示Р的四鄰域,用N4(P)表示。點P的4個對角點與四鄰域一起稱為Р的八鄰域,用N8(P)表示,其中4個對角點的坐標分別為(x-1,y-1 ),(x-1,y+1) , (x+1,y-1),(x+1 ,y+1)。四鄰域與八鄰域的示意圖如圖4所示,圖中灰色區(qū)域表示Р點鄰域。如果2個像素鄰接,則稱這2個像素是連通的,圖4a中灰色區(qū)域與Р點為四連通。
邊緣檢測提取的輪廓基于八鄰域連接且圖像為二值圖,因此可以利用種子填充算法定位檢測區(qū)域,操作步驟如圖5所示:1)在端面區(qū)域內找到一個前景像素點Р作為初始種子,設初始種子為(xmin+(rmax–rmin)/2,ymin)即可,將Р點壓入棧中并做好標記。2)將Р點彈出棧頂,遍歷Р點的上下左右4個鄰域點,如果Р點的鄰域點不是輪廓點(像素值為0)或未被標記,則將該鄰域點壓入棧中并做好標記。3)彈出棧頂鄰域點,遍歷該鄰域點的上下左右4個鄰域點,如果該鄰域點的4個鄰域點不是輪廓點或未被標記,則將該鄰域點壓入棧中并做好標記。
4)重復第3步,直到棧為空,所有鄰域點均被標記。
至此,便已成功提取端面連通域,此連通域即套圈端面區(qū)域(圖6),后續(xù)的缺陷檢測只需處理套圈端面區(qū)域內的圖像,為節(jié)省后續(xù)運算時間奠定基礎。
圖6 端面區(qū)域定位結果
將套圈缺陷分為外形缺陷(大小邊、磕碰傷)和外觀缺陷(車廢、磨傷等端面損傷)。2.1 外形缺陷判別對于外形缺陷,用最小二乘法計算所提取2條套圈端面輪廓的大、小圓圓心,通過圓心距離進行判定。如圖7所示:如果大、小圓的圓心距離dc超過設定的閾值Dmax,則將其判定為大小邊缺陷;如果外圓圓心最短距離dout與外圓半徑rout的差值Δout超過設定的閾值Dout,則將其判定為外圓磕碰傷缺陷;如果內圓圓心最長距離din與內圓半徑rin的差值Δin超過設定的閾值Din,則將其判定為外圓磕碰傷缺陷;
2.2 外觀缺陷判別2.2.1 圖像坐標系轉換套圈端面是一個圓環(huán),直接進行圖像分割會被套圈外的黑色區(qū)域嚴重干擾而無法正確提取缺陷,因此需要將提取的套圈端面進行坐標系變換,將端面圓環(huán)拉伸成便于后續(xù)處理的矩形。局部分割算法可以在變換后的矩形中進行,提取缺陷后再將圖像從極坐標系變換至直角坐標系。如圖8所示,點P的x,y坐標分別表示其距離原點O的水平距離與垂直距離;點P’的坐標u,v分別表示點Р在圖8a中相對圓心(rx,ry)的極角與極徑。
為避免變換后的矩形圖像長寬比過大并提高圖像處理速度,指定變換后的矩形長為L,寬為H,設定極角比例因子μθ為2π/L,極徑比例因子μl為(R–r)/H。對于直角坐標系Р點到極坐標系P’點的轉換,數(shù)學對應關系為
得到Р點與P‘點的對應坐標后,便可以將P’點的灰度值設置為Р點最鄰近插值,其關系式為
式中:f’(u,v)為矩形P’點的像素值;f(x,y)為原圖中Р點的最鄰近插值。圓環(huán)拉伸成矩形的轉換效果如圖9所示,將圓環(huán)拉伸成矩形后,對矩形圖的缺陷進行提取。
在矩形圖中利用圖像分割提取缺陷后,為便于判定,需要將缺陷轉換到圓環(huán)中,極坐標系轉換為直角坐標系的對應關系為
同理,得到P點與P’點的對應坐標后,便可以將Р點的灰度值設置為P’點灰度值,即
由于轉成極坐標系時會造成部分像素點丟失,在重新轉換為直角坐標系時不一定會有對應的像素點,而如果直接選取與坐標值距離最近的像素點進行轉換可能會造成失真,因此,在尋找P’點像素值時需要運用雙線性插值進行轉換。雙線性插值是在水平方向與垂直方向運用2次線性插值的方法。如圖10所示,P’點為轉換后的未知點,其坐標(u,v)不一定為整數(shù)值,距其最近的4個整數(shù)點為Q11(u1,v1),Q12(u1,v2),Q21(?u2,v1?),Q22(u2,v2)。首先,在v軸方向根據(jù)P’點的v軸坐標值進行插值,在Q11,Q12中插人R1點,在Q2l,Q22中插入R2點;然后,根據(jù)P’點的u軸坐標值與插入的R1點、R2點在u軸方向插入P’點。P’點像素值的計算公式為
通過雙線性插值將拉伸后的矩形(圖9b)重新轉換為圓環(huán)的效果如圖11所示。
2.2.2 圖像分割圖像分割是指利用圖像中的灰度、紋理、空間等特征,將圖像細分為子區(qū)域并突出這些子區(qū)域對自身的相似性及對其他子區(qū)域的不連續(xù)性,最終提取出感興趣的區(qū)域。圖像分割的效果直接決定了后續(xù)特征分析的難度與檢測系統(tǒng)的質量。因此,需要針對檢測目標找到最合適的分割方法。經(jīng)過大量試驗對比,選擇Sauvola局部二值化算法12進行圖像分割。計算以點(x,y)為中心的窗口模板內的灰度均值m(x,y)與標準方差σ(x,y) ,則點(x,y)的閾值T(x,y)為
式中:R為標準方差的動態(tài)范圍,本文檢測對象為八位灰度圖,故R取128;k為調整系數(shù),Sauvola算法的優(yōu)點在于k的微小變化不會顯著影響二值化的結果。利用Sauvola局部二值化算法對車廢、磨傷、無缺陷但光照不均這3種情況進行分割試驗,調整系數(shù)k取0.08,分割效果如圖12所示。
2.2.3 基于多特征的外觀缺陷識別在完成缺陷分割后,由于生產狀況、光照不均等外部因素的影響,有可能存在噪聲區(qū)域或偽缺陷區(qū)域,需要對分割后的圖像進行圖像特征統(tǒng)計與分析,根據(jù)分析結果進行缺陷判別。如圖12a所示,車廢缺陷區(qū)域與端面正常區(qū)域相比,其灰度值較低且一般沿著圓周方向分布于端面上。因此,選取區(qū)域面積S、區(qū)域輪廓長度L、最小外接矩形主軸至圓心距離D作為車廢缺陷的判別特征。判別示意圖如圖13所示。提取出缺陷區(qū)域后可以計算出該缺陷的最小外接矩形與該外接矩形的主軸直線公式,Ax+By+C=0于是小圓圓心(x0,y0)至主軸直線的距離D為
提取出缺陷后,計算該缺陷的區(qū)域面積S與區(qū)域輪廓長度L,如果缺陷面積與輪廓長度皆未超過設定閾值,則視為無此類型缺陷轉而進行下一缺陷的識別;否則進一步計算最小外接矩形主軸至小圓圓心的距離,由于車廢細化后呈圓弧形,故圓心至主軸的距離會大于小圓半徑,所以將小圓半徑設為距離閾值TD,若距離D超過閾值TD,則將此套圈判定為車廢缺陷。如圖12b所示,磨傷缺陷均分布在端面邊緣靠近大圓處,形狀近似月牙形,且灰度值比端面正常區(qū)域低,因此同樣需要對磨傷缺陷進行特征分析。由于磨傷缺陷邊緣靠近圓心一側近似于一條直線,可以用Hough線變換將這條直線擬合出來。如圖14所示,直線在極坐標系中的表達式為
對于(14)式,可以理解為過點(x0,y0)的直線集有以下表達式
則在極坐標系的極徑、極角平面中,由(15)式所得曲線中的任一點都表示一條過點(x0,y0)的直線。
將圖像中所有的點(xi,yi)代入(14)式中,如圖15所示,如果多個不同的點在極坐標系中得到的曲線相交,便意味著這些點可以連成一條直線。如果同時相交的數(shù)量超過了設定的閾值,則對該直線進行擬合。
找出磨傷缺陷邊緣的直線后,計算缺陷區(qū)域與正常區(qū)域的灰度差進行判別,判別示意圖如圖16所示。利用Sauvola算法分割出磨傷缺陷后,在缺陷邊緣靠近圓心一側利用Hough線變換擬合出直線L1,再將直線向靠近圓心方向平移一定距離(本文取8個像素)得到直線L2,在原圖像端面上提取直線L1遠離圓心一側的區(qū)域S1,以及直線L1與L2之間的區(qū)域S2,計算2塊區(qū)域灰度值均值的差值,差值超過設定闕值即可判定為磨傷缺陷。
為驗證端面缺陷檢測算法的可靠性,在如圖17所示的檢測線上對軸承套圈端面進行缺陷檢測,選取外徑150 mm、內徑90 mm 的33118型軸承套圈樣本1 000個,其中合格品400個、外形缺陷樣品200個(含大小邊、磕碰傷)、車廢樣品200個、磨傷缺陷200個。
在線檢測的統(tǒng)計結果見表1,由表可知:合格套圈出現(xiàn)9個誤檢,仔細觀察套圈表面并分析圖像特征發(fā)現(xiàn)套圈外邊緣在磨削過程中出現(xiàn)了砂輪花,使該部分區(qū)域灰度值偏低且表現(xiàn)相似于磨傷缺陷,故將其誤檢為磨傷缺陷,而砂輪花只影響端面美觀,因此這類誤檢可以接受;車廢套圈與磨傷套圈總共出現(xiàn)5個漏檢,分析后發(fā)現(xiàn)漏檢原因為缺陷較細微,即使是肉眼觀察也不易立刻察覺,此類問題同樣可以接受;系統(tǒng)整體識別準確率達98.60%,而且對于外徑小于150 mm套圈的檢測時長小于600 ms,低于端面磨出料時長,完全能夠滿足企業(yè)生產節(jié)拍和檢測要求。
另外,對不同型號的套圈也進行了多次檢測,識別準確率較高,誤漏檢率較低,響應時間較短,并能實時統(tǒng)計被檢測套圈的型號、數(shù)量、合格率、缺陷種類等數(shù)據(jù),滿足企業(yè)生產在線檢測要求,可以替代人工實現(xiàn)檢測。如果你的工業(yè)生產線中,可能用的到機器視覺或AI深度學習方面的技術來做質量管控,那不妨和我們盈泰德科技聊聊,我們會先根據(jù)你的需求分析,從一個專業(yè)的角度免費來給你設計一個合適你的方案,然后聽取你的意見,再詳細洽談,最后即使沒能達成合作,我們也非常希望能多認識個朋友。